M&M, I think there is another insert or "fix" that addresses the stress concerns , and properly fit will never be seen on a closed gunnel or can be minimally visible on an exposed top wale ( if one chose the insert with the correct grain in the same wood type, stained well and perhaps with some added grain feature ). I will attach some I needed to do on a rare Williams 16 foota ie. 16 of them.
Note: the insert below was some 16-18 inches and I could replace wood all the way to the outer wale surface.
with an open wale you could come from the wale bottom and not sacrifice the top surface and effectively hide the repair and not be concerned with a stress point.
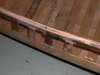
Note: the insert below was some 16-18 inches and I could replace wood all the way to the outer wale surface.
with an open wale you could come from the wale bottom and not sacrifice the top surface and effectively hide the repair and not be concerned with a stress point.
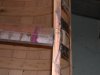
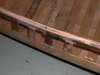