Aesthetics issue
I have had this little aesthetics issue. This being a Huron there is the gapping between the planks, which I don't have an issue with, it adds to the character of the craft. The issue was I could easily see the filler colour between the planks, a bright blue/white and it was distracting to say the least, not something I wanted to see while paddling.
My solution, after experimenting with brushing in the hull colour and other ideas was to apply an acrylic pigment to colour the canvas. I have the pigments from previous painting activities. What I did was thin it really well and then apply it between the planks with a glueing syringe. Any lumps in the mixture would clog the syringe so it needed to be water thin, but that just allowed it to flow really well, sometimes under the ribs to the next visible section.
After application I would just wipe the excess off the varnish. I know it sticks really well to the varnish because I missed cleaning up after some earlier experimenting and it didn't like coming off the varnish. The pigment is designed for use on canvas so I'm just hoping it doesn't soften once it gets wet outside.
It looks much better, the colour I used, Raw Sienna, seems to match the cedar pretty well and I'm quite happy with the results.
In other news, I have the second coat of finish colour on and the stem bands are here, so, I'm hoping to have this project wrapped up next weekend.
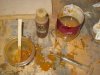
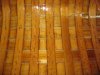
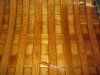