Melthias15
Curious about Wooden Canoes
Hey everyone, at long last I have ripped into the Old Town and I have a couple of updates along with some questions. After getting the canvas off, I saw that the hull was a patchwork of bondo repairs
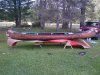
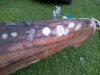
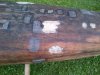
All the the wood, except the planking at the very tips and 2 thwarts, is original. And since this canoe was used for a camp that means that there are at least 13 ribs to be replaced. A fair amount of planking could due with a replacment, but I understand that most of it will be alright except in sections where there is a hole and or a considerable about of rot, such as this:

As usual, stripping the interior was the first step. This being my first restoration, and having limited time on my hands, I decided to only do a single stripping.
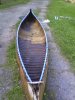
Even with only going over once, the difference was pretty astounding. I also stripped the gunnels and decks, but it seems that they had a layer of red paint under the blue, and it was not being very cooperative. I decided that my priorities were not in getting a perfect finish, but rather in doing structural repairs, and have left the mottled blue/red coat alone for now. After stripping, i decided to get the most terrifying part over with and to tackle the end repairs. The stem in the stern (interesting turn of phrase) was still there, but bairly. The top 6in of the bow stem basically fell apart in my hands. The tip of one deck was rotten but attached, but the other tip was gone, and all four inwale tips were shot.
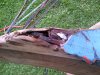
In other words, I needed to bring up three sections of one side to meet the existing stem, and all 4 sections to meet at an imaginary point in space (maybe not that big of a deal for an experienced builder, but it was pretty terrifying to me).
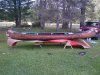
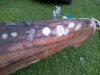
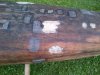
All the the wood, except the planking at the very tips and 2 thwarts, is original. And since this canoe was used for a camp that means that there are at least 13 ribs to be replaced. A fair amount of planking could due with a replacment, but I understand that most of it will be alright except in sections where there is a hole and or a considerable about of rot, such as this:

As usual, stripping the interior was the first step. This being my first restoration, and having limited time on my hands, I decided to only do a single stripping.
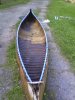
Even with only going over once, the difference was pretty astounding. I also stripped the gunnels and decks, but it seems that they had a layer of red paint under the blue, and it was not being very cooperative. I decided that my priorities were not in getting a perfect finish, but rather in doing structural repairs, and have left the mottled blue/red coat alone for now. After stripping, i decided to get the most terrifying part over with and to tackle the end repairs. The stem in the stern (interesting turn of phrase) was still there, but bairly. The top 6in of the bow stem basically fell apart in my hands. The tip of one deck was rotten but attached, but the other tip was gone, and all four inwale tips were shot.
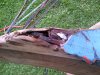
In other words, I needed to bring up three sections of one side to meet the existing stem, and all 4 sections to meet at an imaginary point in space (maybe not that big of a deal for an experienced builder, but it was pretty terrifying to me).