RoadRunner
Enthusiastic about Wooden Canoes
Hey All -
Been awhile since I posted, but I finally took the first-timer's leap and fiberglassed the outer hull of my Freedom 17' from Bear Mountain. While the base 2 coats are well in place and curing up, things didn't go very well in terms of cosmetics. After much consultation with Ron Frenette of Canadian Canoes / Bear Mountain, we decided that the core issue was that I didn't squeegee with much pressure, which allowed ripples to form and at least one major section of the cloth do bubble up a bit on the first coat (notice the cloudy spots in the close up pic - they are definitely raised when I run my hand across the surface).
Naturally, I didn't catch this until well after things had hardened up, so the result isn't pretty (see attached pics.) Ron and I discussed how to approach this - he has some excellent prescriptions in mind - but I also wanted to hear what you guys had to say so that, when I start working on this, I'm armed with as much info as possible. Let me know:
1. Any recommended solutions
2. What steps to take
3. Additional goofs to watch out for
4. How to know if I've done things right (besides the obvious beautiful - if imperfect - canoe finish that I'm looking for).
Thanks guys.
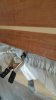
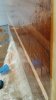
Been awhile since I posted, but I finally took the first-timer's leap and fiberglassed the outer hull of my Freedom 17' from Bear Mountain. While the base 2 coats are well in place and curing up, things didn't go very well in terms of cosmetics. After much consultation with Ron Frenette of Canadian Canoes / Bear Mountain, we decided that the core issue was that I didn't squeegee with much pressure, which allowed ripples to form and at least one major section of the cloth do bubble up a bit on the first coat (notice the cloudy spots in the close up pic - they are definitely raised when I run my hand across the surface).
Naturally, I didn't catch this until well after things had hardened up, so the result isn't pretty (see attached pics.) Ron and I discussed how to approach this - he has some excellent prescriptions in mind - but I also wanted to hear what you guys had to say so that, when I start working on this, I'm armed with as much info as possible. Let me know:
1. Any recommended solutions
2. What steps to take
3. Additional goofs to watch out for
4. How to know if I've done things right (besides the obvious beautiful - if imperfect - canoe finish that I'm looking for).
Thanks guys.
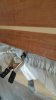
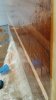