Greg Nolan
enthusiast
There have been a few references on these Forums recently to steam bending using polyethylene tubing instead of a steam box, so Fitz and I thought we would relate our initial experiences with the method.
Fitz and I had both seen the Louis Sauzedde video on steam bending using a polyethylene tube (an industrial product that is used to make polyethylene bags), and both of us thought the method was worth a try. https://www.youtube.com/watch?v=--iPQIwSEJM&app=desktop Fitz did some research and obtained 500 feet of 3 inch 6 mil polyethylene tubing which we shared. The six mil tubing seems stiff, but when heated, it becomes very soft and flexible. I used some of my share of the tubing to steam and bend two ash inwales for the 15’ Old Town 50 pounder that I am restoring. He used some of his to bend the Honduran mahogany outwales on a 1960’s vintage 18 foot Old Town OTCA that he was restoring.
I’ll describe how we went about things, in hopes that it may help others who may wish to try the technique. It will take two posts, because we have a few pictures. If you are tempted to try this process, do look at the Sauzedde video.
My inwales were successfully bent and I expect I will use the process again, but things didn't go too smoothly for me on this first attempt – in good part because the steam source I used, a Wagner wall paper remover (which I believe is the same as the steam generator sold by Rockler), did not produce enough steam for this method. Some people on the forums have used them with apparent success when feeding steam to a traditional steam box.
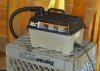
I got the ash for the inwale from Rollin Thurlow and cut it to the proper size and angled shapes. The old damaged inwales I was replacing were still in the canoe – they made an ideal bending jig for the new inwales. The day before bending, I dampened both inwales pretty well as I watered the lawn in the afternoon and evening, and left them in the damp grass overnight.
The next morning I put the first inwale in a length of poly tube and laid it level on the horses on which the canoe was sitting, feeding the steam into one end. This produced two problems. First, most of the steam cooled and condensed before it reached the far end of the tube, so the far end of the new inwale did not get enough hot steam. Second, most of the condensed water stayed trapped in the tube between the two horses instead of draining out. And while the steam cooled as it condensed, the resulting water gathering in the thin tube was very hot, not much cooler than boiling.
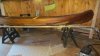
So I rearranged things for a second try – I fed the steam hose about half-way down into the tube, and I set the tube and inwale on a fairly steep slant by raising one end, so the lowered far end would get enough heat and condensed water would drain from the end of the tube:
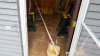
After about 30 minutes of steaming, I pulled the steam outlet back up the poly tube so the raised half of the inwale began to get steam and heat, for about another 40 minutes. Because the wood in the first lower section was already hot, the steam did not condense as much as before, and that wood stayed hot.
I had lots of clamps ready to go on the floor of the canoe, and I had a temporary cross bar clamped at each end in order to induce a bit of over-bend to anticipate and compensate for bend-back:
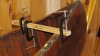
CONTINUED IN PART 2 - NEXT POST
Fitz and I had both seen the Louis Sauzedde video on steam bending using a polyethylene tube (an industrial product that is used to make polyethylene bags), and both of us thought the method was worth a try. https://www.youtube.com/watch?v=--iPQIwSEJM&app=desktop Fitz did some research and obtained 500 feet of 3 inch 6 mil polyethylene tubing which we shared. The six mil tubing seems stiff, but when heated, it becomes very soft and flexible. I used some of my share of the tubing to steam and bend two ash inwales for the 15’ Old Town 50 pounder that I am restoring. He used some of his to bend the Honduran mahogany outwales on a 1960’s vintage 18 foot Old Town OTCA that he was restoring.
I’ll describe how we went about things, in hopes that it may help others who may wish to try the technique. It will take two posts, because we have a few pictures. If you are tempted to try this process, do look at the Sauzedde video.
My inwales were successfully bent and I expect I will use the process again, but things didn't go too smoothly for me on this first attempt – in good part because the steam source I used, a Wagner wall paper remover (which I believe is the same as the steam generator sold by Rockler), did not produce enough steam for this method. Some people on the forums have used them with apparent success when feeding steam to a traditional steam box.
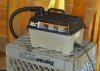
I got the ash for the inwale from Rollin Thurlow and cut it to the proper size and angled shapes. The old damaged inwales I was replacing were still in the canoe – they made an ideal bending jig for the new inwales. The day before bending, I dampened both inwales pretty well as I watered the lawn in the afternoon and evening, and left them in the damp grass overnight.
The next morning I put the first inwale in a length of poly tube and laid it level on the horses on which the canoe was sitting, feeding the steam into one end. This produced two problems. First, most of the steam cooled and condensed before it reached the far end of the tube, so the far end of the new inwale did not get enough hot steam. Second, most of the condensed water stayed trapped in the tube between the two horses instead of draining out. And while the steam cooled as it condensed, the resulting water gathering in the thin tube was very hot, not much cooler than boiling.
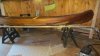
So I rearranged things for a second try – I fed the steam hose about half-way down into the tube, and I set the tube and inwale on a fairly steep slant by raising one end, so the lowered far end would get enough heat and condensed water would drain from the end of the tube:
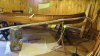
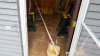
After about 30 minutes of steaming, I pulled the steam outlet back up the poly tube so the raised half of the inwale began to get steam and heat, for about another 40 minutes. Because the wood in the first lower section was already hot, the steam did not condense as much as before, and that wood stayed hot.
I had lots of clamps ready to go on the floor of the canoe, and I had a temporary cross bar clamped at each end in order to induce a bit of over-bend to anticipate and compensate for bend-back:
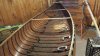
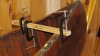
CONTINUED IN PART 2 - NEXT POST
Last edited: